May 2, 2025
Category:
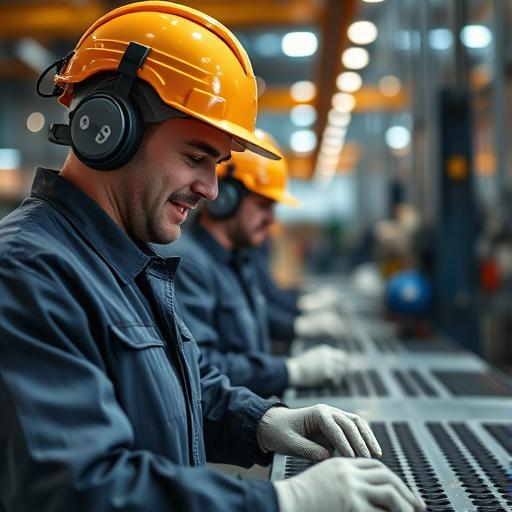
Manufacturing operations face some serious curveballs these days. 😅 Supply chain hiccups, sky-high logistics costs, and tricky communication across continents have pushed companies to seriously rethink their old offshore production habits. Enter nearshoring—moving manufacturing to countries closer to home. It’s proving to be a smart way to balance keeping costs down with making operations more reliable and robust.
We’re going to look at how nearshoring manufacturing operations can give your supply chain strategy a major boost. Think fewer logistical headaches while staying competitive. You’ll get the scoop on the real-world pluses of bringing production closer, what hurdles to expect, and some pointers from companies that have already made the leap. Whether you’re thinking about a full move or just dipping your toes in with a hybrid setup, these insights should help you figure out what makes sense for your business goals.
What Is Nearshoring in Manufacturing?
So, what exactly is nearshoring? At its heart, it’s a strategic approach where companies shift production from faraway lands (think across oceans) to countries that are geographically closer. Often, these nearby countries might share a border, a common market, similar languages, or convenient time zones. It’s different from offshoring (going far away, usually for much lower labor costs) and onshoring (bringing production back to the home country). Nearshoring aims for that sweet spot between affordable costs and convenient proximity.
Think of nearshoring as a way to build a safety net for your supply chain. Moving production closer naturally cuts down on vulnerabilities – like those massive shipping delays we’ve all experienced. While it might not be as cheap labor-wise as some distant offshore spots, it often beats domestic production costs. The big win comes from simpler logistics, quicker turnaround times, and an overall stronger, more resilient operation ready to handle unexpected bumps in the road. 💪 This serves as a valuable risk mitigation strategy.
Why is everyone talking about nearshoring now? Well, a perfect storm of factors has pushed it into the spotlight. Recent global disruptions (hello, pandemic!), shifting customer demands for faster delivery and customization, and leaps in manufacturing technology have all made companies look for smarter supply chain setups. Nearshoring offers a compelling answer to these modern challenges, driving its rapid adoption across the manufacturing sector.
“Nearshoring is a process where companies shift production from overseas to nearby countries that share a market, language, or time zone.” -Optilogic
Key Benefits of Nearshoring Manufacturing Operations
Let’s talk money first. Nearshoring can bring some attractive cost advantages, even if labor isn’t dirt cheap. You’ll likely see savings from shorter shipping routes (lower fuel costs, faster transit!), reduced need for massive inventory stockpiles sitting on boats or in warehouses, and potentially fewer tariffs depending on trade agreements between neighboring countries. It’s about looking at the total cost picture, not just the per-hour labor rate.
Communication gets a whole lot easier too. When your manufacturing partners are just one or two time zones away, scheduling calls doesn’t require waking up at 3 AM. Fewer cultural gaps and language barriers mean smoother collaboration, quicker problem-solving when issues pop up, and faster decision-making between your home base and the production floor. It just makes working together more efficient. 😊
Nearshoring is a huge plus for supply chain resilience. Being closer geographically means your supply lines are less exposed to far-flung global disruptions, whether it’s port congestion, geopolitical instability, or natural disasters halfway around the globe. Lead times shrink dramatically, allowing for more flexible production scheduling. This means you can react quicker to sudden spikes or dips in market demand without waiting weeks for products to arrive.
Quality control often sees a significant improvement with nearshoring. It’s simply easier to keep an eye on things when the factory isn’t a 20-hour flight away. Popping over for facility visits becomes feasible, allowing for better oversight of production processes. This proximity helps ensure more consistent adherence to your quality standards and makes navigating regulatory requirements less of a headache.
“Neighboring countries often have fewer cultural and linguistic difficulties compared to offshoring locations. They usually have shared business practices and less of a language barrier, which leads to smoother relationships and fewer misunderstandings.” -Fictiv
Market Responsiveness and Agility
One of the biggest perks of nearshoring is the speed boost. Having production closer allows companies to react much faster to shifts in the market. Spotted a new trend? Need to adjust production based on sudden demand changes? Nearshoring cuts out those long ocean voyages, giving you a serious competitive edge by getting products to customers or adapting your offerings without those frustrating delays. ⚡
Proximity unlocks exciting possibilities for product customization. Being closer to your end markets makes it much easier to tailor products for specific regional tastes or requirements. Need to roll out a quick design tweak based on customer feedback? Want to offer more personalized options? Nearshoring supports this kind of agility, allowing for faster implementation of changes and more diverse product lines.
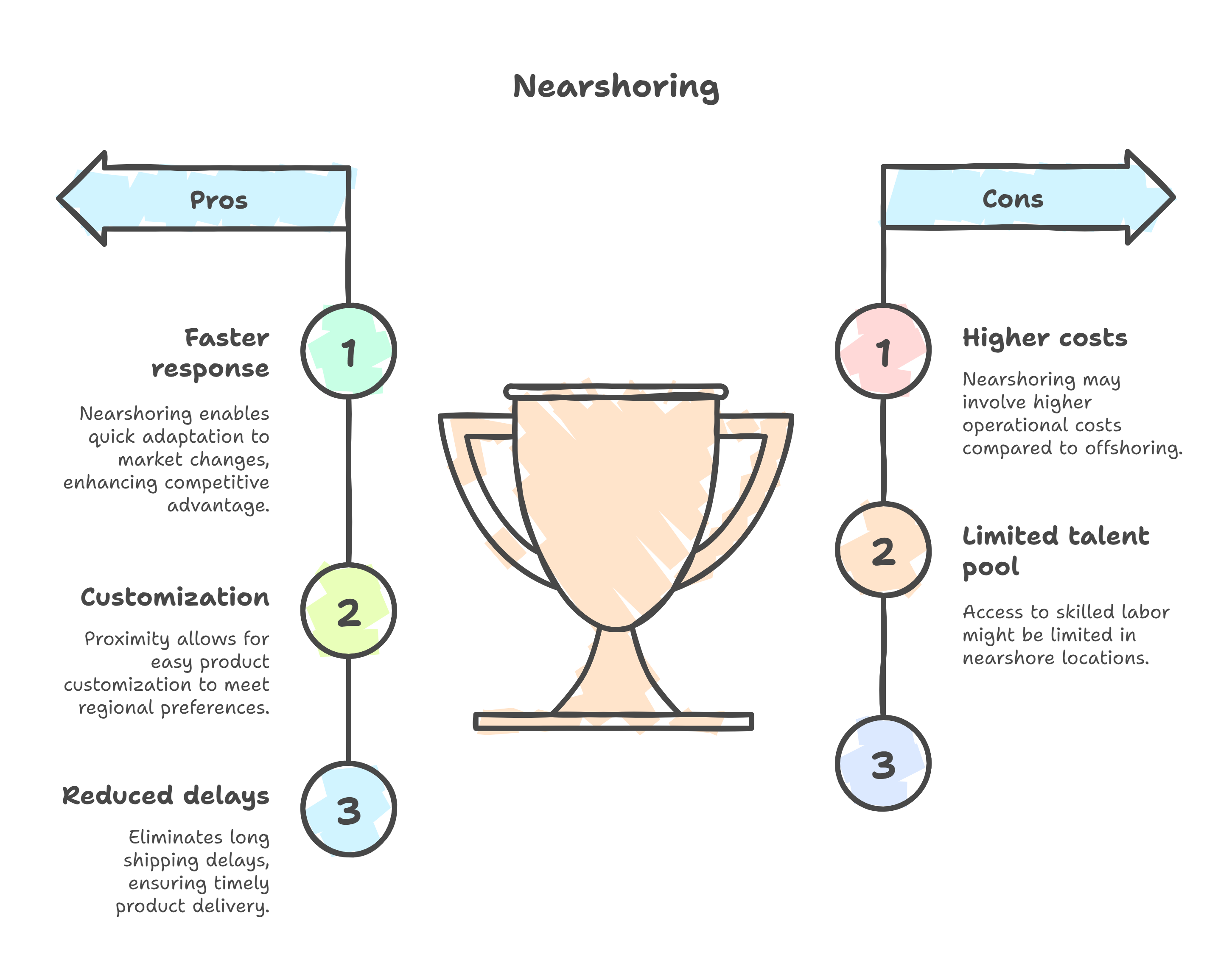
Nearshoring significantly shortens the time it takes to get a product from concept to customer shelf – what’s known as time-to-market. This faster cycle isn’t just about launching new products quickly. It also enables more frequent, smaller production runs. This means you can fine-tune output based on real-time sales data and market feedback, reducing the risk of overstocking or missing out on sales.
“By having production facilities closer to the main markets, companies can reduce lead times dramatically, enabling them to launch products faster.” -Cosmos Sourcing
Cost Considerations and ROI Analysis
Let’s be real: nearshoring involves a cost trade-off. Yes, labor and maybe even facility costs in nearby countries might be higher than in traditional far-offshore locations. But you have to weigh that against the savings. Reduced shipping and logistics expenses, lower inventory carrying costs (less cash tied up!), and potentially lower costs associated with managing risks (like supply disruptions) can make a big difference. The key is to look at the *total cost of ownership*, not just the sticker price of production. 🧐
Calculating the return on investment (ROI) for nearshoring requires a broad view. You need to tally up the measurable savings – things like transportation cost reductions, lower inventory holding expenses, and maybe even faster cash flow because products get to market quicker. But don’t forget the less tangible, yet valuable, benefits: potentially better product quality leading to fewer returns, an improved brand image from more resilient operations, and happier customers getting their orders faster.
Nearshoring can also offer greater long-term cost stability. Offshore manufacturing often leaves companies vulnerable to wild swings in ocean freight rates, surprise tariffs imposed by governments, or unpredictable currency exchange fluctuations. By shortening the supply chain and often operating within more stable economic blocs or trade agreements, nearshoring can shield your business from some of that volatility, making financial planning a bit less uncertain.
“While labor in nearby nations may cost more than in traditional offshoring choices (like China or Vietnam), manufacturers that relocate closer to home often see logistics, energy, transportation, and other operational costs drop in turn.” -Parsec Corp
Operational Control and Quality Improvements
Being geographically closer naturally means better oversight. It’s much simpler (and cheaper!) to send your team for regular site visits when the factory is a short flight away, not halfway across the planet. This allows for closer monitoring of production lines, spotting potential issues earlier, and intervening quickly when problems do arise. It fosters a stronger sense of control over how your products are actually being made.
Quality management often gets a boost with nearshoring. Neighboring countries might share similar quality standards or regulatory frameworks, making alignment easier. Reduced language barriers and time zone differences mean your quality assurance teams can collaborate more effectively with the factory floor. Clearer communication leads to fewer misunderstandings about specifications, resulting in more consistent product quality and fewer defects reaching your customers. ✅
The close proximity fostered by nearshoring strengthens relationships throughout the supply chain. Being in similar time zones allows for real-time conversations and faster problem-solving when snags occur. It helps build stronger, more collaborative partnerships not just with the primary manufacturer but also with their local suppliers. This alignment in business practices and communication styles contributes to a smoother, more integrated operation.
“When quality-related concerns arise, time is of the essence. Waiting until tomorrow morning on the other side of the globe to execute a plan can compound losses by extending downtime, adding to scrap, and wasting energy and team member hours.” -Parsec Corp
Challenges and Potential Drawbacks
Nearshoring isn’t always a walk in the park. Setting up or relocating production involves significant upfront investment – finding facilities, moving equipment, training staff. The transition period itself can cause disruptions to your existing supply chain. And while total cost might be lower, certain ongoing expenses in nearshore locations might still be higher than what you were paying far offshore, requiring careful budget management. These challenges need consideration.
Finding the right skills and sufficient capacity can be tricky. Some nearshore regions, while growing, might not yet have the deep pool of specialized manufacturing talent or the extensive supplier networks found in long-established offshore hubs like China. Infrastructure – like ports, roads, and reliable power – might also be less developed in certain areas, potentially limiting production scale or efficiency.
Navigating the legal and regulatory environment is another hurdle. Each country has its own set of labor laws, environmental regulations, tax policies, and customs procedures. Understanding and complying with these different rules can be complex and requires dedicated effort and often local expertise. Missteps here can lead to costly fines or operational delays.
Protecting your intellectual property (IP) and ensuring consistent quality control are crucial concerns. IP protection laws and enforcement can vary significantly between countries. Likewise, quality standards and oversight mechanisms might differ. Companies need to perform due diligence, select partners with robust systems, and establish strong contractual safeguards and monitoring processes to mitigate these risks. 🛡️
“Even the best companies can struggle in new environments. For example, Taiwan Semiconductor Manufacturing Company (TSMC) has successfully built many semiconductor fabs in Taiwan but has faced higher costs and longer timelines in Arizona due to differences in permitting and labor standards.” -Bain & Company
Strategic Implementation Approaches
Jumping into nearshoring doesn’t have to be an all-or-nothing plunge. Many companies find success with a phased approach. This might mean starting by moving the production of less complex products or only certain manufacturing processes to the nearshore location first. This allows you to test the waters, learn the ropes, build relationships, and iron out kinks with lower risk before committing to a larger-scale transition.
Another popular strategy is the hybrid or “split-shoring” model. This involves keeping some production in existing offshore locations (perhaps for high-volume, stable products where cost is paramount) while developing nearshore capabilities for newer products, customized items, or those needing faster market response. This blended approach aims to capture the best of both worlds – cost efficiency *and* supply chain resilience.
Choosing the right nearshore manufacturing partner is absolutely critical. Don’t just look at price! Key factors to assess include their technical capabilities and experience with your type of product, their quality management certifications and track record, their financial stability and long-term viability, their communication infrastructure, and perhaps most importantly, their cultural fit and willingness to collaborate closely with your team. 🤔
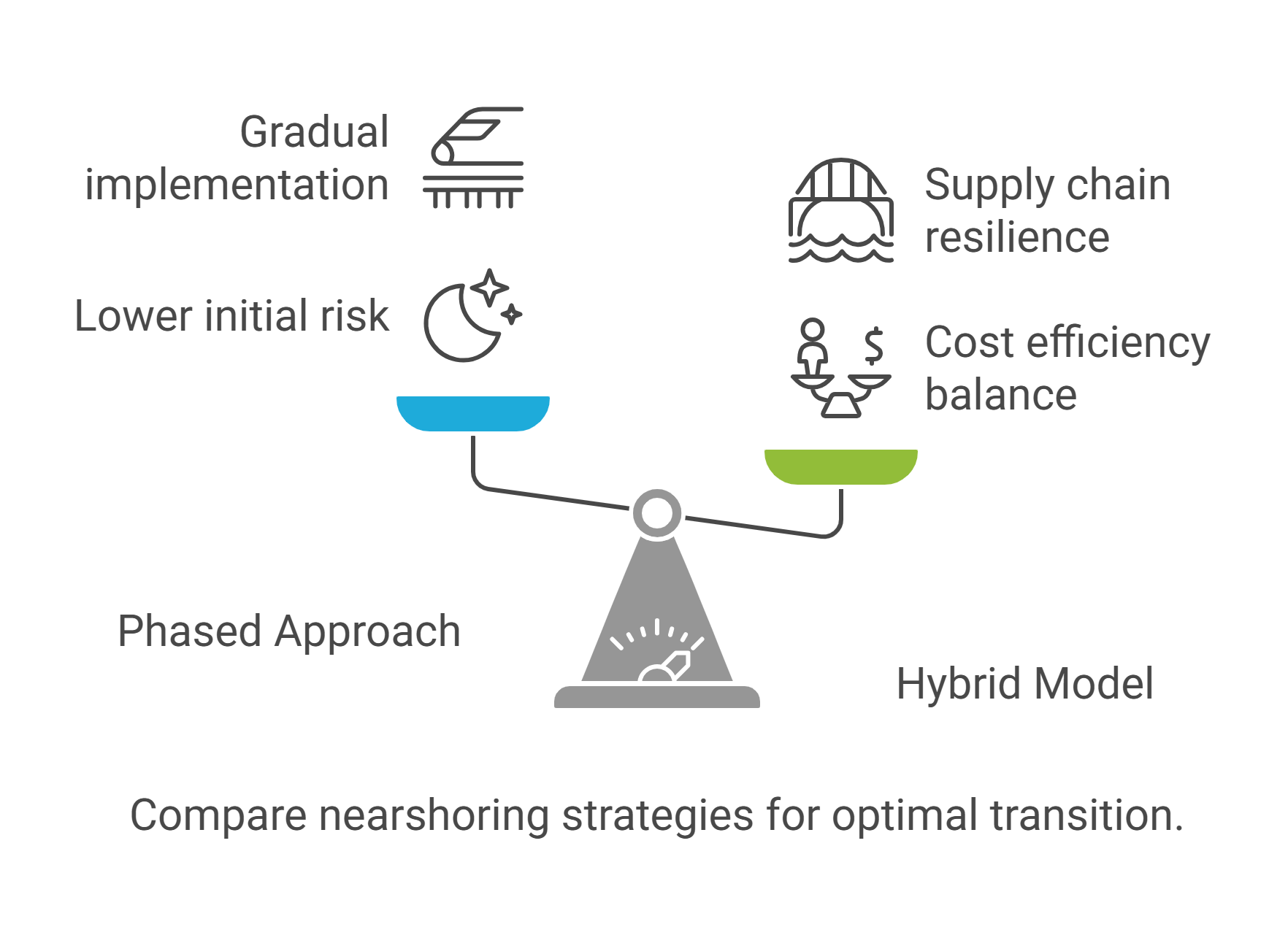
“Our research shows the most common strategy today is split-shoring, or combining nearshoring and offshoring strategies to balance resilience and cost challenges.” -Bain & Company
Supply Chain Visibility and Integration
Knowing what’s happening across your entire supply chain is vital. While nearshoring simplifies the *physical* chain by shortening distances, you still need robust systems for visibility. This means tracking not just your direct manufacturing partner (Tier 1) but also their key suppliers (Tier 2, Tier 3, etc.). Without this end-to-end view, you’re still vulnerable to disruptions hiding further down the line.
Integrating technology smoothly between your headquarters and your nearshore facilities is a common challenge. You need compatible systems for things like inventory management, production scheduling, quality reporting, and financial tracking. Ensuring consistent data formats and reliable communication protocols is essential for seamless information flow, enabling informed decisions and efficient collaboration across locations.
A nearshoring initiative can be a fantastic catalyst for broader digital transformation. As you’re setting up or refining nearshore operations, consider investing in smart factory technologies. Things like automation, IoT sensors for real-time monitoring, and advanced data analytics can turn your nearshore facility into a highly efficient, intelligent, and responsive production hub, amplifying the benefits of proximity. 💡
“While many companies have improved traceability for Tier-1 suppliers, most face significant gaps in tracking Tier-3 suppliers and beyond. Without comprehensive visibility, companies face increased risk of disruptions, inefficiencies, and compliance failures.” -Bain & Company
Sustainability and Environmental Considerations
Nearshoring can be a win for the planet too! 🌎 Shorter transportation distances mean significantly fewer miles traveled for raw materials and finished goods. This directly translates to a lower carbon footprint from shipping, helping companies meet their environmental goals and reduce greenhouse gas emissions associated with their supply chains.
Beyond just carbon emissions, nearshoring can boost resource efficiency. Less time in transit often means less need for excessive protective packaging. Reduced reliance on long-haul air freight (which is very energy-intensive) and ocean shipping contributes to lower overall energy consumption. It’s a move towards a leaner, less resource-intensive supply chain model.
Stakeholders are paying attention to environmental impact. Consumers increasingly prefer brands perceived as sustainable, investors are factoring environmental, social, and governance (ESG) criteria into decisions, and regulators are tightening environmental standards. Nearshoring provides a tangible way for companies to demonstrate environmental responsibility and align with these growing expectations, often while improving operational performance.
“Shorter supply chains mean reduced transportation costs and inventory needs, faster response times, increased agility in changes in demand and an alignment with consumer preferences for more localized production.” -Industry Week
Regional Nearshoring Opportunities
For companies based in North America, Mexico is the dominant nearshoring destination. Its geographical proximity, established manufacturing base (especially in automotive and electronics), relatively lower labor costs compared to the US/Canada, and favorable trade agreements like the USMCA make it a compelling choice. Many regions boast skilled labor and growing infrastructure.
Western European businesses often look eastward for nearshoring opportunities. Countries like Poland, the Czech Republic, Romania, and Hungary offer advantages such as a well-educated and skilled workforce, competitive labor costs (compared to Western Europe), solid logistics infrastructure, and the benefits of operating within the European Union’s single market and regulatory framework.
In Asia, companies looking to diversify away from China or serve regional markets are exploring Southeast Asian nations. Vietnam, Thailand, and Malaysia, for instance, offer proximity to major East Asian economies like Japan and South Korea. They provide established manufacturing capabilities in various sectors, competitive costs, and growing domestic markets.
Don’t overlook Central and South America as emerging nearshoring hubs, particularly for North American companies. Countries like Costa Rica (known for medical devices and electronics), Colombia (textiles, BPO), and Brazil (diverse industrial base) are actively developing their manufacturing sectors and infrastructure to attract foreign investment, offering alternative options beyond Mexico.
“These benefits resonate with operations leaders and customers, investors and stakeholders increasingly focused on environmental impact and regional economic growth.” -Industry Week
Case Studies and Success Stories
Consider a major automotive supplier that faced constant disruptions shipping components from Asia. By shifting a significant portion of its production to Mexico, it slashed lead times by over 70%, reduced logistics costs by nearly 30%, and gained much greater flexibility to adjust production schedules based on fluctuating North American automaker demands. Quality consistency also improved due to easier oversight.
A mid-sized electronics company struggled with long development cycles and communication barriers with its distant offshore partner. They adopted a hybrid nearshoring approach, moving final assembly and testing for their North American market to Costa Rica while keeping component manufacturing offshore. This move cut their time-to-market for new products by half and allowed for quicker responses to quality issues, ultimately boosting customer satisfaction despite managing the transition with a lean team.
Even small businesses can make nearshoring work. A niche apparel brand wanted faster turnarounds for smaller, fashion-driven collections. Instead of setting up their own facility, they partnered with a specialized nearshore manufacturer in Guatemala that catered to smaller clients. This allowed them to produce smaller batches quickly, respond rapidly to trends, reduce inventory risk, and build a reputation for fresh, timely designs without massive upfront investment.
Working with Nearshoring Partners
Selecting the right partner is arguably the most critical step in a successful nearshoring venture. Look beyond the basics. Assess their specific technical expertise relevant to your products. Scrutinize their quality management systems (QMS) and certifications. Check their financial health and stability – you want a long-term partner! Evaluate their communication tools and responsiveness. And consider the cultural fit – will you be able to build a strong, trusting relationship?
Once you’ve chosen a partner, building a strong working relationship is key. This isn’t just a transactional arrangement. Foster open and regular communication – scheduled calls, clear reporting formats. Establish shared Key Performance Indicators (KPIs) so everyone is working towards the same goals. Develop joint processes for tackling problems when they arise. Building trust and collaboration takes effort but pays huge dividends in smooth operations.
Navigating the shift to nearshoring manufacturing operations can feel complex, but you don’t have to go it alone. This is where specialized expertise comes in handy. Nearshorely focuses specifically on helping companies make this transition successfully. They offer expert guidance, help identify and vet the right manufacturing partners in ideal locations, assist with planning the transition smoothly, and provide ongoing support to ensure your nearshoring strategy delivers results. Check them out for specialized services.
Future Trends in Manufacturing Nearshoring
Technology will continue to shape nearshoring. Expect to see more advanced automation, robotics, and AI-driven quality control being deployed in nearshore facilities. Digital twins and sophisticated planning software will improve coordination between headquarters and nearshore plants. These technologies make nearshore locations even more competitive by boosting efficiency and capability.
Supply chain strategies are becoming more sophisticated. The trend is moving away from relying solely on one location (offshore or nearshore) towards building more flexible, resilient networks. This might involve a mix of nearshoring, some strategic offshoring, regional distribution hubs, and even localized micro-factories, all connected and optimized using data analytics for maximum agility.
Geopolitics and economics will always play a role. Shifting trade policies, efforts towards regional economic self-sufficiency, rising global shipping costs, and security concerns will likely continue to encourage companies to shorten supply chains and favor nearshoring. Expect regions to actively compete for nearshoring investments through incentives and infrastructure development.
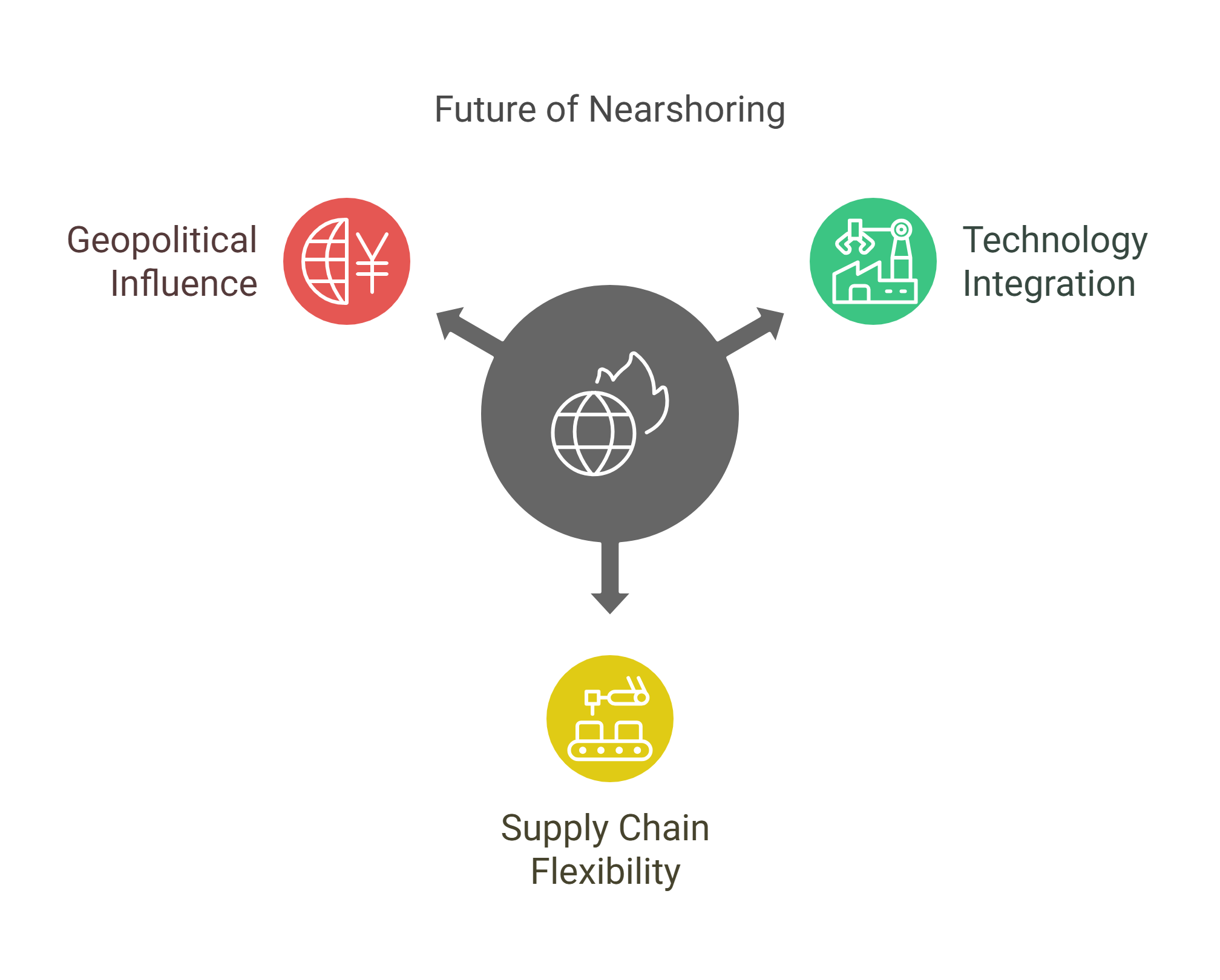
FAQ: Common Questions About Nearshoring Manufacturing
What is the difference between nearshoring and offshoring in manufacturing?
The main difference is geography! Nearshoring means moving production to a country close to your home market (like Mexico for the US, or Poland for Germany). Offshoring typically sends production much farther away (like to China or Vietnam from the US/Europe), usually chasing the lowest possible labor costs. Nearshoring often balances cost savings with benefits like shorter shipping times, easier communication due to similar time zones, and potentially lower geopolitical risks.
How do I calculate the true cost of nearshoring my manufacturing operations?
Look beyond just the labor rate per hour! To get the true picture, calculate the *total cost of ownership*. This includes the direct costs (labor, materials, factory overhead), but also logistics (shipping, customs, duties), inventory carrying costs (more inventory needed for longer supply lines), quality management expenses (travel, inspection, potential rework), transition costs (setup, training), and risk management factors (cost of potential disruptions). A comprehensive view often shows nearshoring is more competitive than it first appears.
What are the biggest challenges companies face when implementing nearshoring?
Key challenges often include finding nearshore partners with the right specific skills and capacity, managing the initial investment and potential disruption during the transition phase, ensuring consistent product quality standards are met, navigating different regulatory environments (labor laws, environmental rules, taxes), and setting up systems for effective communication and supply chain visibility across locations. Careful planning and partner selection are crucial for overcoming these.
How long does it typically take to transition to a nearshore manufacturing model?
There’s no single answer, as it depends heavily on factors like the complexity of your products, the scale of the operation being moved, your industry’s specific requirements, and whether you’re setting up your own facility or working with a partner. A rough estimate could range from 6 months to 2 years or more. Key phases include initial research and strategy, partner selection/site setup, pilot production runs, and gradually ramping up to full operational capacity.
Is nearshoring suitable for all types of manufacturing operations?
Not necessarily. Nearshoring tends to offer the biggest benefits for products where speed-to-market is important, demand fluctuates, customization is needed, shipping costs are a major factor (bulky/heavy items), or close collaboration/oversight is critical (complex assembly, high quality requirements). For very high-volume, standardized products where labor cost is the absolute dominant factor and lead times are less critical, traditional offshoring might still make sense. It requires evaluating your specific business needs.
Conclusion
Nearshoring manufacturing operations isn’t just a trend; it’s a strategic realignment offering a powerful blend of cost-effectiveness and geographical advantage. In a world where supply chains face constant tests, the benefits of shorter logistics paths, smoother communication, tighter quality control, and nimble operations make nearshoring a seriously compelling choice for manufacturers everywhere. Yes, challenges like transition costs, partner vetting, and regulatory navigation exist, but with smart planning and the right help, companies can unlock major competitive gains.
Deciding to nearshore requires a deep look at your specific operational setup, market dynamics, and future business direction. Nearshorely specializes in guiding companies through this intricate process. They provide expert advice, help pinpoint ideal partners, and offer hands-on support for implementation, all shaped around your unique situation. Whether you’re thinking of a full move or a strategic mix, the Nearshorely team can help you tackle the challenges and reap the rewards of bringing production closer. Visit https://www.nearshorely.com/ today to see how their specialized services for nearshoring manufacturing operations can reshape your strategy and set your business up for lasting success in today’s unpredictable climate.
Key Takeaways:
- Nearshoring balances cost efficiency with supply chain resilience by relocating manufacturing to neighboring countries
- Benefits include reduced logistics costs, improved communication, faster market response, and enhanced quality control
- Successful implementation requires thorough cost analysis beyond just labor rates to understand total value
- A phased or hybrid approach can minimize disruption while maximizing advantages
- Partner selection and relationship management are critical success factors in nearshoring initiatives
- Technology integration and supply chain visibility systems are essential enablers of effective nearshoring
- Environmental benefits include reduced carbon footprint and alignment with sustainability expectations
- Working with specialized partners like Nearshorely can significantly improve transition outcomes
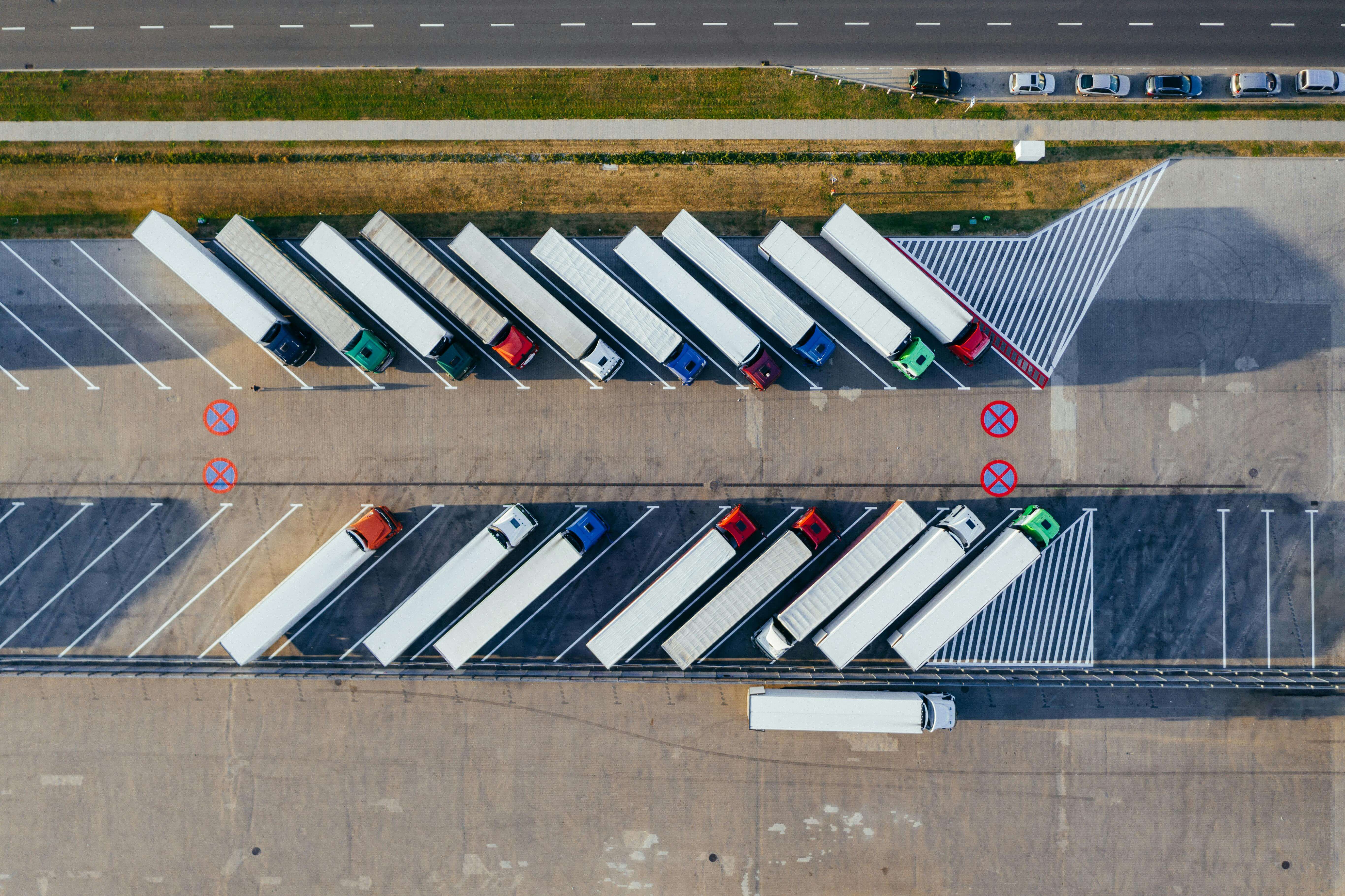
Services